Ventajas del corte plasma frente al oxicorte
El corte plasma presenta ciertas ventajas sobre el proceso de oxicorte que pasamos a detallar a continuación:
- La utilización de cortes por plasma conlleva la generación de una cantidad reducida de residuos, una menor deformación del material y una zona afectada por el calor de dimensiones menores.
- Al operar a velocidades de corte significativamente superiores, el proceso de corte por plasma sobrepasa al oxicorte, incluso al no considerar el tiempo requerido para el precalentamiento ni las acciones secundarias asociadas al oxicorte.
- Al distribuir los gastos operativos entre un mayor número de unidades por hora y reducir la duración de las actividades complementarias, se obtiene como consecuencia un costo inferior por cada pieza.
- La obtención de mayores utilidades para su empresa se deriva de la combinación de un costo operativo reducido y una productividad ampliada.
- No es necesario regular gases ni supervisar sustancias químicas inflamables, y tampoco se requiere mantener ninguna distancia de separación.
- El proceso de corte por plasma es capaz de trabajar con acero al carbono, aluminio, acero inoxidable, cobre y la mayoría de las demás aleaciones metálicas. Es adaptable para realizar cortes manuales, mediante un sistema de rieles, en tuberías o en una superficie de corte X-Y. Además, tiene la capacidad de cortar láminas metálicas apiladas, estructuras de metal con rejillas e incluso componentes con óxido o pintura.
- No requiere gases inflamables adicionales. Los sistemas Powermax® funcionan exclusivamente con aire comprimido como su único gas necesario. A diferencia del oxicorte, que utiliza acetileno como el gas combustible principal, un gas altamente inflamable y de naturaleza inestable.
En Exel Air contamos con sistemas Powermax® de corte plasma de la marca Hypertherm, ideales para cualquier aplicación industrial
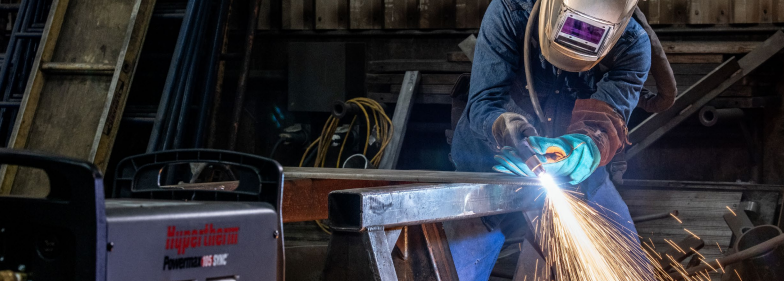